For years, the concept of sustainable manufacturing was something of an oxymoron – the traditional manufacturing industry being a heavy consumer of energy, water and other resources, while producing high volumes of waste. A combination of regulation, legislation and consumer demand, however, has seen the industry make real strides in recent times in meaningfully reducing its environmental footprint and developing truly sustainable practices.
According to Pat O’Hara, managing director at Architectural & Metal Systems (AMS), sustainability is undoubtedly a growing priority for the manufacturing sector.
“Consumers are increasingly demanding products that are made ethically and sustainably,” he says. “At the same time, the climate and environmental crisis is pushing manufacturers to reduce carbon emissions and incorporate recyclable/circular materials.”
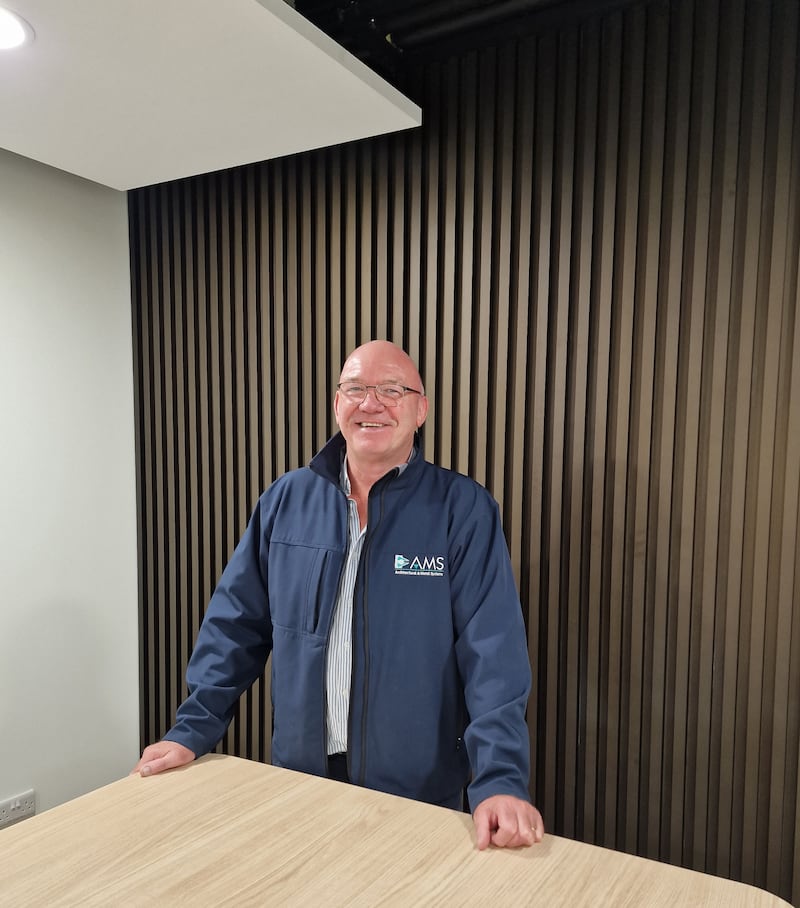
O’Hara also notes that the energy price volatility of recent years has pushed many in the sector to adopt renewable technologies to reduce long-term costs and increase resilience.
SEAI can take you step by step on your home energy upgrade journey
Supporting its people in career progression is a key selling point for Bristol Myers Squibb as a great employer
Navigating the future: Ireland’s economic reinvention in a changing world
How legacy companies can thrive in a rapidly changing world
Indeed, many manufacturers appear to be tackling the problem of sustainability from all angles. Ronan Guest, EY partner in supply chain and operations, highlights several notable ways in which the manufacturing sector is focusing more on sustainability, including focusing on energy efficiency, both in machinery and processes. For example, he says, Siemens and General Electric are employing smart technology to reduce waste and energy usage.
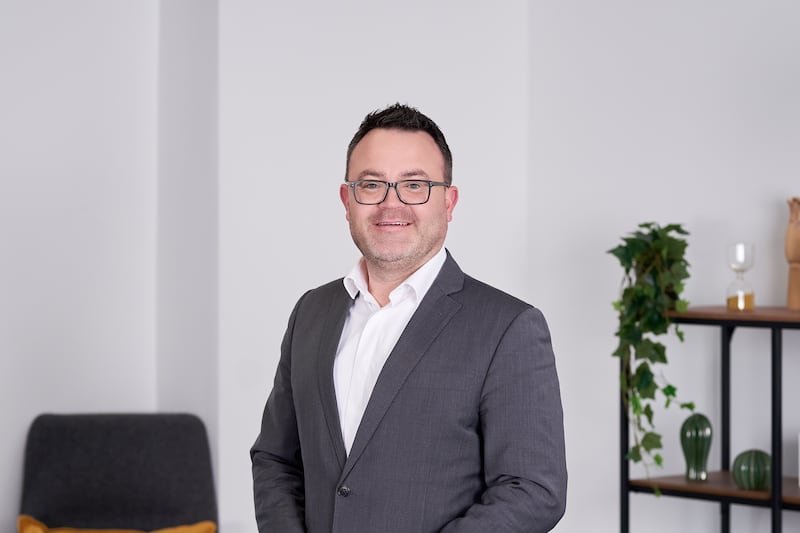
The circular economy is also gaining prominence, Guest notes, with a focus on reusing materials and reducing waste: “This includes moves by larger fast-moving consumer goods companies towards the use of recycled material in their packaging and avoiding single-use plastics.”
Water conservation is a particular priority in the textile industry, the second biggest consumer of water globally. Leading brands such as Levi Strauss are now implementing water-saving technologies in production processes.
Supply-chain transparency has also come to the fore, says Guest; the market leaders are the brands that provide detailed information about their suppliers and manufacturing processes.
Yet Áine Brassill, supply chain and operations transformation partner with PwC Ireland, says the organisation’s 2024 global supply chain survey found that in reality few big companies have adapted their supply chains to be more compliant regarding environmental, social and governance (ESG) matters.

Although companies must comply with various ESG regulations, such as the European Union‘s Corporate Sustainability Reporting Directive, and pending EU supply chain regulations, just 12 per cent of the organisations surveyed reported being fully compliant, although this rose to 63 per cent among market leaders. Brassill points out that growing regulation in the area is posing new challenges.
“More than 40 per cent of surveyed companies recognise that making their supply chains more ESG compliant is highly disruptive now and in the future,” she says. “Since the start of the year, however, we have noted that some companies are reviewing their ESG plans given the changing geopolitical environment and recent European Commission Omnibus package, which seeks to protect SMEs from excessive sustainability information requests. Others are, however, continuing to push ahead.”
Guest points out that many Irish manufacturers rely on global supply chains, which can complicate attempts to implement more sustainable practices. And it doesn’t come cheap, he adds: “Without external funding, some businesses will struggle to secure the capital required to focus on more energy efficient production methods. Moreover, if businesses’ costs increase in response to the need to meet emissions targets, this may need to be passed on to consumers.”
Many in the industry say more targeted support is needed if manufacturers are to meet ambitious climate targets and fulfil often onerous regulatory requirements. O’Hara says more support from the Government would make a significant difference, particularly when it comes to setting clear standards and aligning policy with sustainability goals.
“One of the key challenges we face is that there’s often a disconnect between sustainability ambitions and procurement practices, particularly in the construction sector,” he notes. “While there’s growing awareness around carbon reduction, the frameworks that govern material selection and project approval don’t always support or incentivise sustainable choices.”
Stronger Government action – such as clearer low-carbon procurement guidelines, tax incentives for greener materials, or stricter emissions standards – could help level the playing field, he says.
“It would empower manufacturers who are investing in cleaner processes and allow sustainability to compete on more than just cost.”
AMS has invested heavily in renewable energy and resource efficiency across its operations. A one-megawatt solar panel system comprising 2,500 panels has been installed as the first phase of a larger four-megawatt solar project, and the company has also implemented a rainwater harvesting system to reduce dependence on mains water and improve overall sustainability.
It sources metal with a high recycled content, as well as procuring primary aluminium from smelters powered by renewable energy.
“These initiatives reflect AMS’s commitment to embedding energy efficiency and environmental responsibility throughout its manufacturing processes,” says O’Hara.
Yet he believes that one of the main challenges the manufacturing sector faces in reducing its environmental footprint is the pressure to compete on price, noting that manufactured goods are often highly price sensitive.
“At AMS, we produce a wide range of finished and semi-finished aluminium products, and we sometimes lose out on projects where the decision comes down to the lowest upfront cost,” he admits.
Unfortunately, when price is the primary driver, sustainability often takes a back seat. “Lower-cost materials frequently have a higher environmental impact, especially in terms of embodied carbon, and may come from less regulated or carbon-intensive supply chains,” says O’Hara. “This undermines efforts to promote greener alternatives, even when they offer clear long-term environmental benefits.”