On the flat plains of Lower Saxony, near the town of Salzgitter, a new empire is growing out of the land. Well, specifically out of the mud right now, as it’s been raining for the past couple of days and, like all building sites, it doesn’t take long for the muddy puddles to form.
Once the mud is clear and replaced by concrete and steel, this 260,000sq m site will be the home of Volkswagen’s first battery “gigafactory”, which has become something of a buzzword of late, applied to any production site that just happens to be large.
This is, or at least in due course will be, a factory for making gigas. Gigawatts of power, packaged in batteries destined for Volkswagen’s fleet of new electric cars, and indeed any customers for such parts that it finds along the line.
Speaking of parts, the design and management of the factory is actually under the auspices of Volkswagen Components, the part of the car-making giant that also packs up and sends out the spare parts for your 10-year old Golf. Components is a far bigger business than it sounds, though – it’s worth some €40 billion to Volkswagen, so the €2 billion investment needed in Salzgitter to make the battery factory is getting on for small change. Even so, a whole separate division within VW Components, called Power Co, has been set up so that it can act like a start-up, and make the sort of rapid decisions and fast-developing business plans needed so that VW can keep up in the battery power race.
It’s part of a €30 billion investment in battery technology, research, and construction over the next seven years to deliver a target of 80 per cent of Volkswagen’s sales, worldwide, being made up of electric cars by 2030. In Ireland and the rest of Europe, that figure is more like 100 per cent, although with the recent lobbying to water down the proposed EU ban on combustion engines, that may change in the interim.
Eventually the plan is to increase production to 40gWh per year, enough batteries for 500,000 electric cars
Salzgitter has been part of the VW empire for some time now. The factory on the site started in 1970, making the somewhat unloved K70 hatchback and saloon, a precursor to the first-generation Passat. By 1975, Salzgitter had been refitted to make petrol engines, and it’s been doing that ever since.
Now, the plant that made engines is turning over to making batteries instead. There’s already a pilot production plant on the site, a section of the factory that once made cylinder heads and which is now making experimental batteries for the next-generation of electric cars and vans.
The gigafactory that’s currently rising, to an eventual height of 60m, out of the Saxon mud will have a capacity of 10-gigawatt/hours (gWh) for each of its two large production halls. Eventually the plan is to increase production to 40gWh per year, enough batteries for 500,000 electric cars. That’s just a small part of what VW needs to build all those new EVs though – the company estimates that it needs some 240hWh of battery production by 2028, so Salzgitter will be joined by further Gigafactories in Valencia, in Sweden and in Ontario.
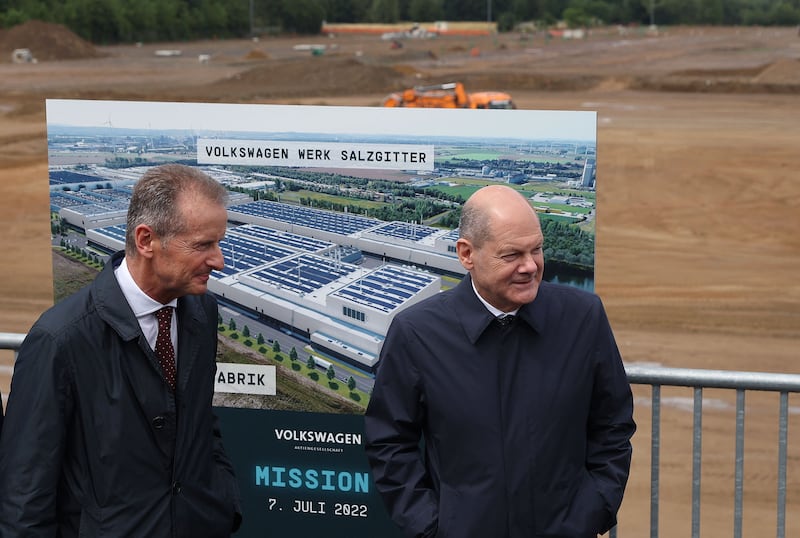
Why all this frantic battery factory construction? Because VW doesn’t want to be beholden to Asian battery makers any more. For the current ID electric car line-up, VW mostly buys its batteries from the likes of China’s CATL and Korea’s LG Chem – both dominant players in the world’s battery market.
Well, not for much longer if VW can help it. By switching to designing and making its own batteries, VW wants not only to end its reliance on outside suppliers, it also stands to make dramatic savings.
[ What happens when your EV battery finally runs out of power?Opens in new window ]
“One of the most important things is vertical integration,” says Thomas Schmoll, group board member for Power Co. By that he means getting involved in everything from mining to gathering up old batteries for recycling. “You have to care about the critical minerals, because 80 per cent of the cost of the battery is in the raw materials.”
To help bring down those costs, VW, through Power Co, is doing what VW traditionally, does best – sharing.
Sharing, in this context, is not merely caring, it’s also about money saving. Back in the 1990s, with four mainstream car brands – VW, Seat, Skoda, and Audi – to juggle, VW came up with the idea of platform sharing. By using the same basic set of mechanical components, from engines to suspension to electronics, you could make four cars for only slightly more than the price of one. So, the VW Golf was, essentially, identical to the Skoda Octavia, Audi A3, and Seat Leon under the skin, but you could sell them to four different buyers, maximising your return on the original development investment.
VW hopes to cut the cost of making its batteries by as much as 30 per cent per gWh, compared with current designs
VW refined the platform-sharing art across its various models and marques, so that now a practical seven-seat Multivan is, in purely mechanical terms, very much the same as a compact Golf hatchback. The same is true of VW’s electric cars, all of which ride on the same MEB electric car platform, enabling VW to make the ID.3, ID.4, ID.5, ID.7, ID.Buzz, Skoda Enyaq, Supra Born, and Audi Q4 e-tron all from the same basic box of bits.
Now, VW is applying this technique to batteries, coming up with what it calls the Unified Cell Design. What is it? Well, to look at it seems very much like a slim hardback book. It’s quite heavy when you pick it up though, holding as it does 181 carefully interleaved layers of copper anode and aluminium cathode. These layers – each only microns thick – are where the battery holds its electrical charge. Combine enough of these Unified Cells and you have a battery pack for an electric car.
Indeed, you have a battery pack for lots of different electric cars, because the idea is that the basic layout of the Unified Cell can be adapted to different needs. For 80 per cent of production, the plan is to use relatively simple “iron phosphate” battery chemistry. In theory, this is a good thing – iron phosphate batteries are faster-charging and longer-lived than conventional lithium-ion batteries, but there are downsides – mostly that they don’t hold as much charge for a given weight, meaning their energy density is lower. It could mean that mainstream electric cars owners will have to get used to more frequent, but faster, charging in return for lower prices.
However, iron phosphate batteries won’t cut the mustard for more high-performance applications, such as for Audi and Porsche models, but the Unified Cell can cope with that simply by altering the chemicals that are mixed into a slurry (that’s the official term), which is then applied to the delicate metal foils that make up the cathode and anode. By increasing the content of both manganese and silicon, VW says that it can create more high-performance, but also more expensive, batteries on the same production line.
All of which adds up to cost savings. VW hopes to cut the cost of making its batteries by as much as 30 per cent per gWh, compared with current designs. It’s also looking for a similar reduction in the amount of energy needed to create the battery in the first place, as well cutting the time it takes to develop new batteries in half. The Unified Cell design is said to be future-proof, and VW’s engineers say it can be easily adapted to the much-touted “solid state” battery designs, which aim to improve battery energy and dramatically reduce charging times. VW hasn’t given a timeline for its switch to solid-state batteries, but rival Nissan says it will have them on sale by 2028. VW’s battery team ripostes to that by claiming that the Unified Cell is already 90 per cent of the way to solid-state, and only uses a small amount of liquid electrolyte to allow its power to flow back and forth.
VW says it wants to close the production loop entirely, just as have most smartphone makers, using only tiny proportions of freshly mined raw materials
There are serious concerns about the energy used to mine the materials to make all these batteries, as well as the human rights concerns surrounding large mining operations. To that, Volkswagen’s Frank Blome, Power Co’s chief executive, says: “I think it’s too early to talk about this, but we want to manage the full supply chain and have it under our control. And of course we want to do as much recycling as possible. We can reclaim up to 99 per cent of the minerals from our batteries to be reused.”
A place to do all that is, also, rising from the Saxon mud in Salzgitter. By 2025 the Unified Cell should be in production. At some as-yet-undefined point beyond that, the recycling centre should be in full swing reclaiming the raw materials to make new batteries from old. Eventually, VW says it wants to close the production loop entirely, just as have most smartphone makers, using only tiny proportions of freshly mined raw materials.