The last two years have been extraordinary for Pfizer, according to Paul Reid, the biopharmaceutical company’s country manager in Ireland. “None of us would have predicted that we would have an approved vaccine that would be supplied across the globe, not in millions but in billions of doses, which is quite incredible,” he admits.
Yet Reid believes their biggest success has been the evolving culture at the organisation. “Colleagues are now feeling more empowered,” he says. “They are feeling encouraged to think big, and they are working together to ensure that we can deliver breakthrough medicines that will change people’s lives because ultimately that’s our purpose.”
This sentiment is concretely realised within Pfizer’s Environmental, Social, and Governance (ESG) strategy, which outlines how the company aims to address what they see as their responsibilities within the context of climate change, global health and health equity. The Pfizer ESG strategy includes six priority areas: product innovation, equitable access and pricing, product quality and safety, equity and inclusion, climate change and business ethics.
Equity is a core Pfizer value, and we believe that better health is possible for everyone everywhere. All people deserve access to high-quality, safe, and effective healthcare solutions. To this end, the company also recently announced a unique project called Accord, which is a first-of-its-kind initiative to enhance access to innovative medicine in 45 lower income countries.
READ MORE
“We are seeking to close the equity gap by addressing the challenges that prevent access to innovative vaccines and medicines,” Reid explains. This includes a commitment to provide all of Pfizer’s current and future patent-protected medicines available in the US or EU on a not-for-profit basis – a move that will impact 1.2 billion people. “It is only a start but will hopefully over time have a huge impact.”
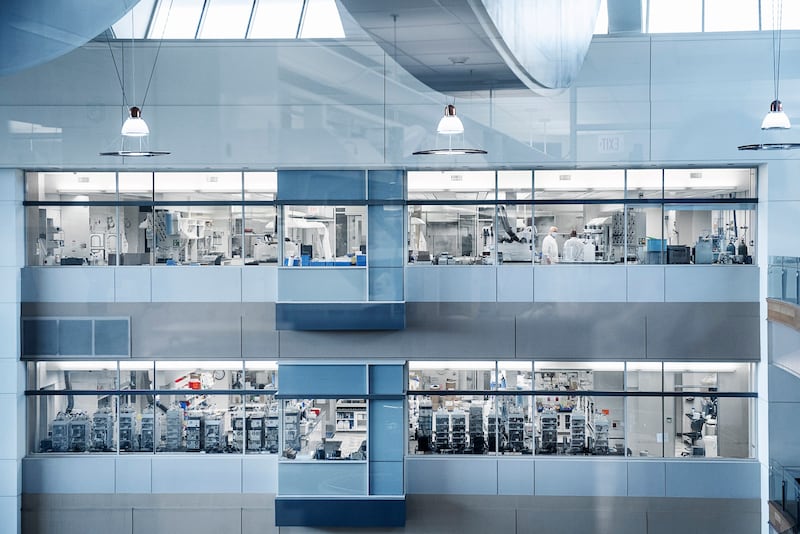
Each of Pfizer’s three manufacturing sites – Grange Castle, Ringaskiddy and Newbridge – has colleagues working in the ESG space on a range of projects as the Irish sites work to achieve the company’s sustainability goals.
Brian O’Neill is energy manager at Grange Castle, and he tells The Irish Times that the site’s energy programme has matured significantly over the past decade. O’Neill is responsible for energy and water reduction projects, and he says that over the past eight years the site has managed to “decouple” energy from production output. He explains: “While our production has steadily increased, we have in fact reduced our carbon emissions and energy usage.”

A number of projects are responsible for this, O’Neill says. For example, the energy team has also worked closely with their colleagues to introduce smarter controls around heating ventilation and air conditioning (HVAC) systems. “This consisted of various innovative control strategies such as introducing setback control so when people leave the building, these things automatically switch off.”
A more sophisticated Fault Detection system was recently deployed that allows the team to know when HVAC systems are running inefficiently, which has resulted in big savings, O’Neill adds. “This saved us over €130,000 in the first six months alone – it is a really innovative tool.”
O’Neill says the team have worked with many energy consultants over the years to identify energy waste and opportunities for savings. In his opinion, there are two aspects to making sure a large production facility such as the one at Grange Castle achieves significant energy reductions. “You can implement projects, but you have to maintain and manage the equipment that is there - if you don’t, you will see energy drift and you can’t improve what you don’t measure.”
More recently, as an organisation Pfizer has made its sustainability intentions clear by committing to become carbon neutral across its internal operations by 2030. Over the next number of years, the focus will be on implementing energy reduction initiatives and the addition of more on-site renewables. Green energy will be procured while decarbonising heat is a priority.
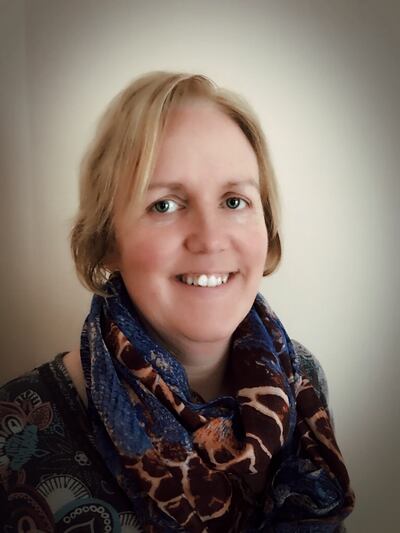
Annette Lynch, a senior research engineer at the Ringaskiddy site, was integrally involved in a novel biodiversity project that saw Pfizer rehabilitate an island in the Cork Harbour area. It was originally built for the nesting of a migratory bird (the common tern), but in recent years flooding caused by spring tides had resulted in nests and eggs being destroyed. “No fledglings have managed to hatch on the island since 2017, which was a big concern,” she explains.
Pfizer worked closely with Cork County Council, the National Parks and Wildlife Service and Birdwatch Ireland on the project, which was done in conjunction with the Ringaskiddy Clinical Manufacturing Facility works to aid their Leadership in Energy and Environmental Design (LEED) certification.
The goal of the project was to raise the island by a metre, which Lynch explains was far from straightforward.
“We had to build a roadway out to the island to bring in stone and machinery, which then had to be removed when the work was finished. All the original rocks that were on the island were removed and then replaced in the original position they had been in so that it would look similar to the birds so they wouldn’t be upset,” she says. They also built a fence around the island to ensure that otters could not disturb the nests.
The entire project took almost 12 months of planning and two weeks to execute. “For the biodiversity team on site, this is the biggest project we have done,” Lynch says. The terns have returned from Africa and several are currently nesting on the island.
Michael Hannigan, engineering lead, utilities and site services at Pfizer’s Newbridge site, was the lead on a novel project to design and construct their osmotic facility with a view to being awarded LEED certification.

“We engaged third-party consultants to guide us through the certification process and to conduct integrated building performance modelling (IBPM), which developed a baseline energy consumption model for the facility based on the LEED standard and then assessed the proposed model against this,” explains Hannigan. “There are prerequisites that must be achieved along with a points score that determines the grade of certification awarded. We were awarded the maximum number of points available under the ‘optimise energy performance’ category, on the basis of how much energy savings we made and what we did from a sustainability perspective.”
The facility achieved a staggering 37 per cent reduction on the baseline energy predictions, which Hannigan says was primarily delivered through heating water using low-grade heat from its combined heat and power (CHP) plant. “This significantly reduced our natural gas consumption.”
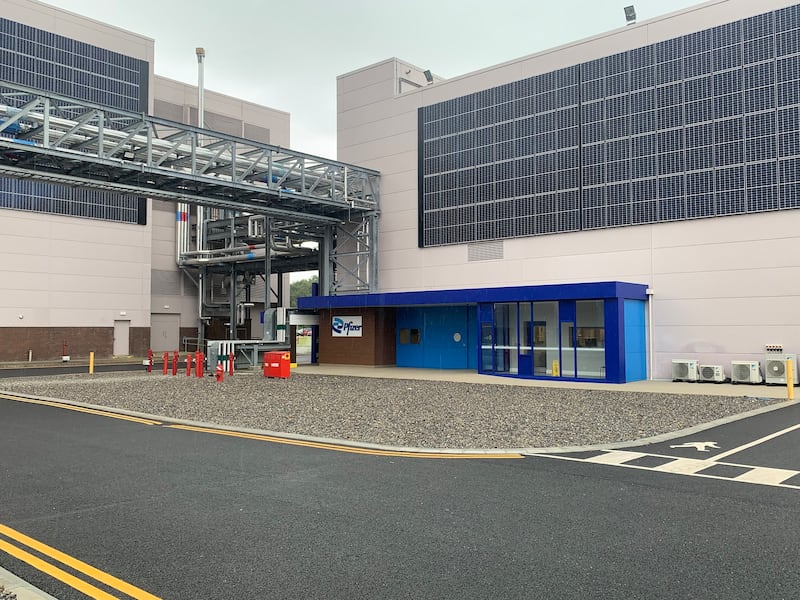
Smart control valves allowed for sophisticated energy monitoring, while the air handling unit was a novel design for the site where only the fresh make-up air was dehumidified rather than the recirculated air. Photovoltaic panels were also installed on the building to supply some of the electrical load. This was all hugely challenging, Hannigan admits, given the redevelopment was completed during the Covid-19 lockdowns. It also represented a massive learning curve but is an approach that will now be replicated across Pfizer sites nationally and internationally.
“This project aligns with our carbon neutrality targets but it also changed how projects were done by incorporating the energy element into it from the design stage, which was a new way of working for us on site.”